Here ya go. When torquing the cylinder head, start in the middle and work your way out in a circle so the head gets tightened down evenly. I usually start with 50% of the given value the first time around and increase it to 75% the second time and 100% the third time around. Tightening it down in stages will help prevent warping the head.
Note: This chart shows 5-7 and 8-10 Ft Lbs for the smaller motors. A torque wrench calibrated in inch pounds should be used for these motors as it will give greater accuracy. So that would be 60-84 and 96-120 Inch Lbs.
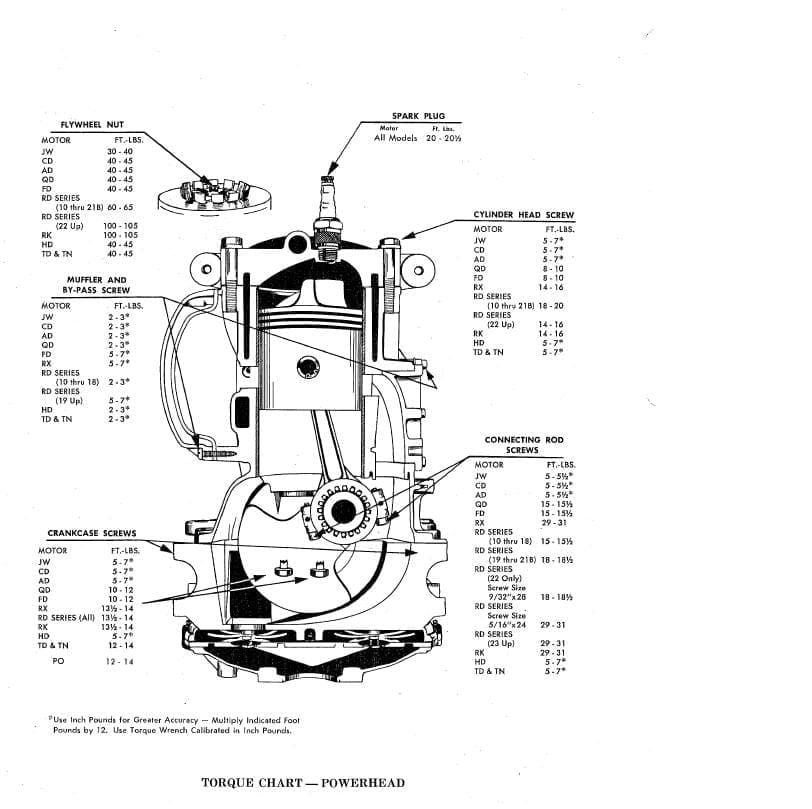